RESINE UV, COME UTILIZZARLE AL MEGLIO
Gli incollaggi industriali stanno diventando via via più importanti nei processi produttivi e sempre più spesso costituiscono una valida alternativa ad altre più complesse tecnologie di giunzione. I vantaggi dell’incollaggio possono essere compresi solo se il relativo processo applicativo è completamente chiaro e quindi efficace. Di seguito alcuni principi fondamentali per lavorare con adesivi UV.
Per scegliere l’ adesivo più adatto non devono essere presi in considerazione solo i requisiti di ingegneria di processo – vale a dire la tipologia di polimerizzazione – ma anche i requisiti tecnici e il carico operativo che si richiedono all’adesivo, non ultime le condizioni di test a cui sottoporlo. A tal riguardo la base chimica dell’adesivo gioca un grande ruolo.
Se si parla di adesivi UV, ci si riferisce solo alla loro metodologia di polimerizzazione, ma non alla loro composizione chimica. La maggior parte di tali adesivi sono realizzati su una basa acrilata o epossidica.
I vantaggi degli adesivi a base epossidica rispetto a quelli acrilati sono soprattutto nella loro eccellente forza adesiva e affidabilità, a cui va aggiunta una maggiore resistenza all’umidità ed agli agenti chimici e una bassa diminuzione di volume compresa tra 1 e 5%. Questo porta ad un bassa tensione residua, che a sua volta favorisce l’adesione.
Con poche eccezioni gli adesivi a base epossidica e polimerizzazione UV induriscono grazie anche alla presenza di cationi. I cationi producono il cosiddetto polimero vivente che, anche senza irraggiamento UV, agevola la polimerizzazione dell’adesivo anche in aree non raggiungibili dai raggi UV.
Il grafico riportato mostra come entro 24 ore la resistenza al taglio di una resina epossidica cationica si raddoppi dopo un trattamento UV per 30 secondi a causa dell’apporto cationico post-polimerizzazione. Ciò è importante se la misure di resistenza al taglio vengono utilizzate per valutare e confrontare le performance dei collanti. L’utilizzatore deve sapere se sta testando un adesivo ad indurimento cationico che viene solitamente selezionato laddove il contesto operativo preveda incollaggi in zone d’ombra difficilmente raggiungibili dai raggi UV.
Rispetto a collanti tradizionali, quelli a polimerizzazione UV dispongono del vantaggio di fotoiniziatori cationici che non possono essere inibiti dall’ossigeno. Inoltre polimerizzano ulteriormente se stimolati termicamente.
Con l’apporto di calore si ottiene infatti un alto grado di reticolazione, superiore a quello conseguito dalla sola polimerizzazione UV.
La polimerizzazione UV iniziale tuttavia è un requisito essenziale per i migliori risultati in combinazione con tale stimolazione termica.
Un elevato grado di reticolazione comporta una temperatura di transizione vetrosa più alta, una maggiore tenuta del collante e resistenza all’umidità e ad agenti chimici più estesa.
Quando si utilizza una sorgente di raggi UV adatta, settata secondo parametri ottimali, gli adesivi UV possono polimerizzare nel giro di pochi secondi o al massimo un minuto. La scelta di una sorgente UV adatta ad un particolare tipo di adesivo è un prerequisito per un processo di successo.
Ci sono differenze nel tipo di lampada o spettro UV che esse coprono. Ci sono differenze significative tra l’efficacia di una lampada a LED o una lampada a vapori di mercurio (Lampada Hg). Una sorgente di raggi Hg emette uno spettro ultravioletto esteso. In una lampada a LED d’altro canto, vi sono lunghezze d’onda predefinite per esempio 365, 385 o 405 nm. Poiché non tutti i fotoiniziatori abbisognano solo di raggi di tali lunghezza d’onda, la polimerizzazione sotto una fonte di luce a LED può non risultare ottimale per molti tipi di adesivi UV.
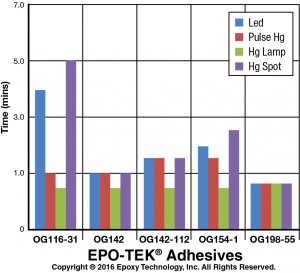
Diversi tipi di resine reagiscono in maniera differente a diversi tipi di sorgenti UV. Ad esempio la resina epossidica EPO-TEK OG 116-31 (sulla sinistra) polimerizza molto velocemente con una lampada UV a irraggiamento diffuso, assai più lentamente con una lampada UV a irraggiamento spot.
Diversi tipi di resine reagiscono in maniera differente a diversi tipi di sorgenti UV. Ad esempio la resina epossidica EPO-TEK OG 116-31 (sulla sinistra) polimerizza molto velocemente con una lampada UV a irraggiamento diffuso, assai più lentamente con una lampada UV a irraggiamento spot.
Una polimerizzazione inadeguata con scarse proprietà finali potrebbe essere il risultato.
Con le lampade Hg è però fondamentale selezionare accuratamente sia lo spettro che il filtro. Per tutte le sorgenti luminose si pone la domanda se utilizzare lampade a irraggiamento diffuso oppure a spot.
Una lampada Hg ad irraggiamento diffuso produce un certo calore sul substrato del collante, ciò promuove la polimerizzazione dei prodotti catationici.
Infine gioca un ruolo importante anche l’intensità UV e la distanza della sorgente dalla zona di incollaggio. E’ buona norma munirsi di un radiometro, così da poter misurare efficacemente la quantità di energia realmente irraggiata nella zona di polimerizzazione della resina.
Inoltre, lo spessore dell’adesivo (bond line) polimerizzato deve essere tenuto in considerazione. Spesso per polimerizzare strati di resina consistenti (> 25 micron), si ricorre alla soluzione di aumentare l’intensità della sorgente di luce UV. Con ciò si ottiene il risultato opposto: lo strato superiore risulterà troppo polimerizzato mentre i raggi UV, riuscendo a penetrare solo parzialmente all’interno del collante, non riusciranno a polimerizzare efficacemente gli strati più interni.
SU Epoxy Technology Inc.:
Dal 1966 l’azienda statunitense Epoxy Technology produce, con il marchio commerciale EPO-TEK, adesivi epossidici per l’industria. I prodotti EPO-TEK eccellono in alcuni campi applicativi quali l’elettromedicale la micro ed optoelettronica, aerospaziale, Telecom, industria dell’ottica.